Danone's Academy Wants To Train 20,000 AI-Ready Workers
AI upskilling
gettyDanone is turning its Opole, Poland, nutrition plant into more than a model factory. It’s making it the heart of a global training push. By 2026, the dairy and beverage giant says up to 20,000 frontline workers across its global network will be trained to use AI tools, cobots, and digital twins. The initiative, known internally as the Industry 5.0 Academy, aims to build the kind of skills that are in short supply.
Coined by European policymakers and industry analysts, Industry 5.0 extends the Industry 4.0 playbook of sensors, data lakes and robotics by putting people at the center of advanced manufacturing. Danone argues that AI cannot deliver its full value unless factory teams are confident prompt-writers, data interpreters and cobot partners.
That shift isn’t theoretical. Around the world, manufacturers are looking to find workers who can interpret data, write prompts, or collaborate with AI systems. The problem isn’t just hiring, it’s retraining the workforce already in place.
“The global manufacturing sector faces a significant shortfall of skilled workers,” says Vikram Agarwal, Danone’s chief operating officer. “It’s a commercial imperative for us to train our existing talent base and empower them to be active participants in Industry 5.0. Technologies like AI and robotics are already reshaping how we operate, but their true potential lies in the hands of our people.”
Danone’s Academy program splits the learning into manageable pieces. Workers get micro-lessons on writing better prompts, analyzing sensor data, and using digital assistants. In-person and virtual workshops at Opole are blended with VR simulations and five-minute videos pushed to 130 sites around the world.
The content is grounded in real work. Maintenance teams learn how to describe a machine issue to an AI co-pilot. Line leaders practice using sensor data to tweak production and cut waste. And digital assistants walk through standard procedures, flagging issues before they become expensive problems.
Opole already has a track record with advanced tech. In 2022 the World Economic Forum named the plant a Global Lighthouse after it reduced change-over times by one-third and cut water use 22 percent through use of AI for process controls . Danone is now using the same crew, technicians, line leaders, even hourly workers, as peer trainers for colleagues in Brazil, Indonesia and beyond.
The pace of AI development isn’t slowing. That’s why companies like Danone are treating training as an urgent priority.
Every time AI capabilities improve, the skills needed to use it shift too. Workers in roles that once looked stable, such as customer service, planning, even packaging, are finding their daily tasks automated or redefined.
The numbers back that up. The World Economic Forum says nearly 60% of workers will need new skills by 2027. About 44% of today’s core competencies will become obsolete in the same time frame. And one in four jobs is likely to change or disappear altogether.
At the same time, the upside is significant. McKinsey estimates that generative AI could unlock $2.6 trillion to $4.4 trillion in value each year. But only if the people running the systems know how to harness them.
Danone isn’t alone in linking AI to frontline capability.
Nestlé has rolled out its own internal large language model called NesGPT, designed to speed up product development and troubleshoot production issues. Thousands of staff, from engineers to packaging specialists earn “prompt certificates” after a short internal course.
Unilever, meanwhile, is pushing its AI-enhanced Manufacturing System to more than 120 plants worldwide. The company says early pilots delivered double-digit improvements in equipment efficiency.
Procter & Gamble recently worked with academic researchers to quantify AI’s impact internally. The end result showed that AI provided a significant boost to innovation and employee productivity.
Upskilling employees isn’t just an HR line item, it’s an insurance policy. Teams fluent in AI and automation can adapt faster during supply-chain shocks, plug cyber holes before they widen, and feel less tempted to jump ship for “cooler” tech gigs. For Danone, bringing those skills into Opole now means every future plant upgrade, whether it’s a cobot, a digital twin or the next-gen data stack, can be brought to the factory floor already primed to work on the very first shift.
“The Academy is just the beginning,” Agarwal claims. “We are also creating a new network of 10 pioneering factories to pilot disruptive models of the Digital Factory of the future. Our ambition is to set new industry standards for human-machine collaboration, so we can better serve our customers, consumers and patients around the world”
AI can cut costs, boost speed, and enable new products. But the biggest gains may come from something more basic: giving people the skills to make the tools worth using.
As companies race to invest in digital capabilities, the winners won’t be the ones with the flashiest algorithms, but the ones whose workers know how to put them to work on day one.
Recommended Articles
Danone becomes official partner of CAF reaffirming its commitment to health through food, sports - MyJoyOnline

1
Danone becomes official partner of CAF reaffirming its commitment to health through food, sports

1
Company becomes sixth corporate partner alongside AB InBev

No Hype - just the Facts. Your complete source of news and realtime quotes from the TSX, TSX-V, CSE, CBoe Canada, Montre...
Fan Milk marks 65 years of spreading joy

Fan Milk Ghana, a Danone company that operates in the diary and beverage industry, has been urged to leverage the Africa...
French Company To Expand Presence in Nigeria Despite Exit of Multinationals
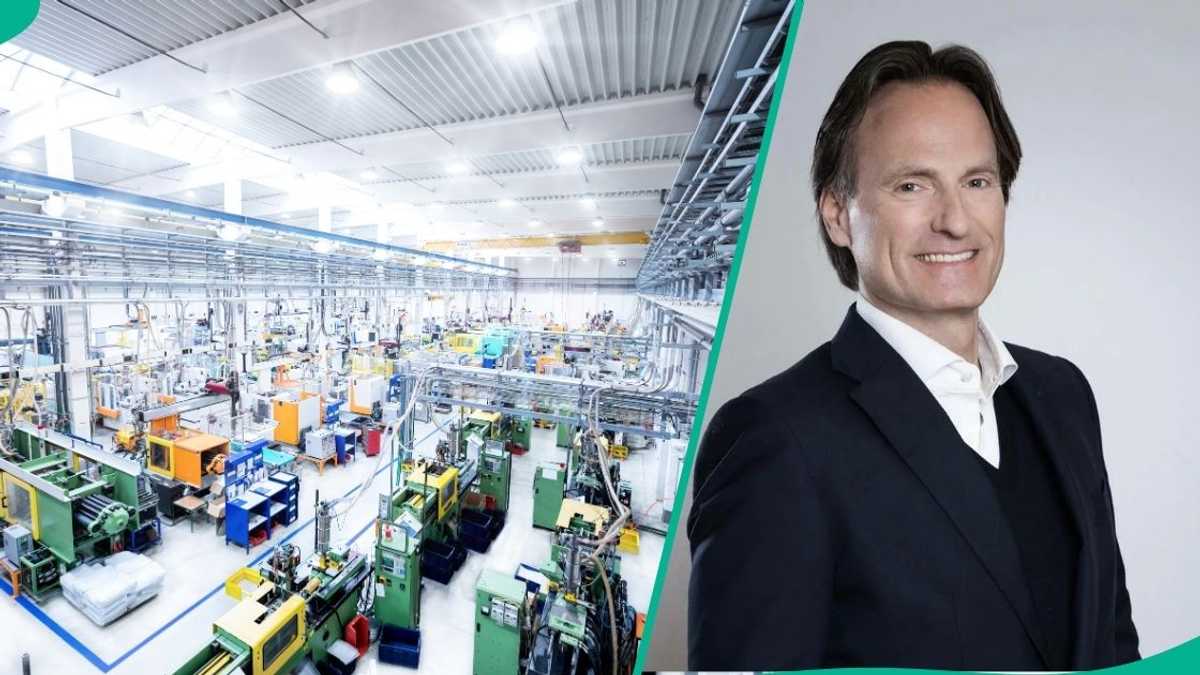
Despite the exit of several multinationals in recent years due to naira devaluation and other economic challenges, a Fre...
You may also like...
Diddy's Legal Troubles & Racketeering Trial
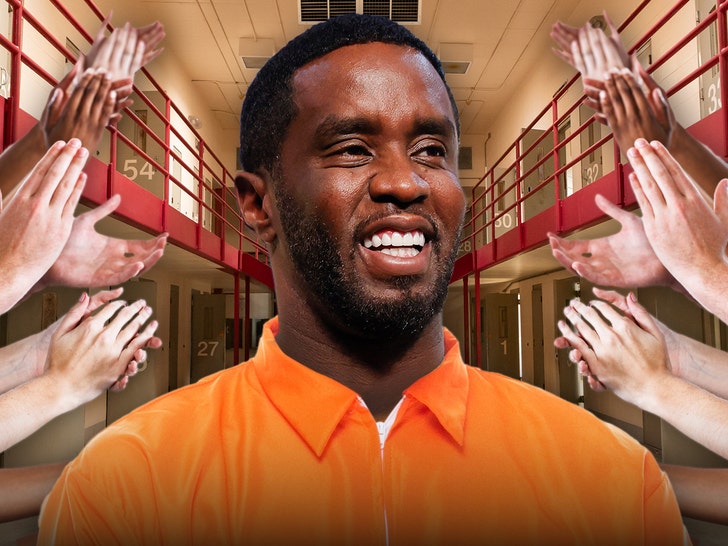
Music mogul Sean 'Diddy' Combs was acquitted of sex trafficking and racketeering charges but convicted on transportation...
Thomas Partey Facing Rape & Sexual Assault Charges

Former Arsenal midfielder Thomas Partey has been formally charged with multiple counts of rape and sexual assault by UK ...
Nigerian University Admission Policy Changes
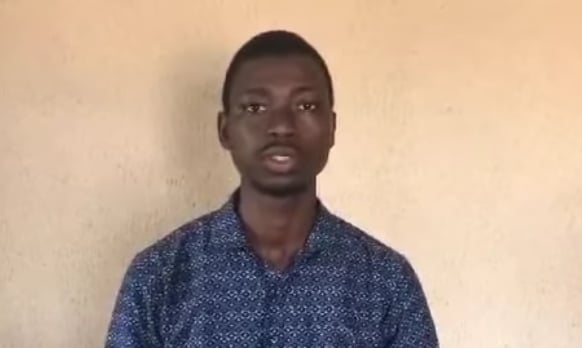
JAMB has clarified its admission policies, rectifying a student's status, reiterating the necessity of its Central Admis...
Ghana's Economic Reforms & Gold Sector Initiatives

Ghana is undertaking a comprehensive economic overhaul with President John Dramani Mahama's 24-Hour Economy and Accelera...
WAFCON 2024 African Women's Football Tournament
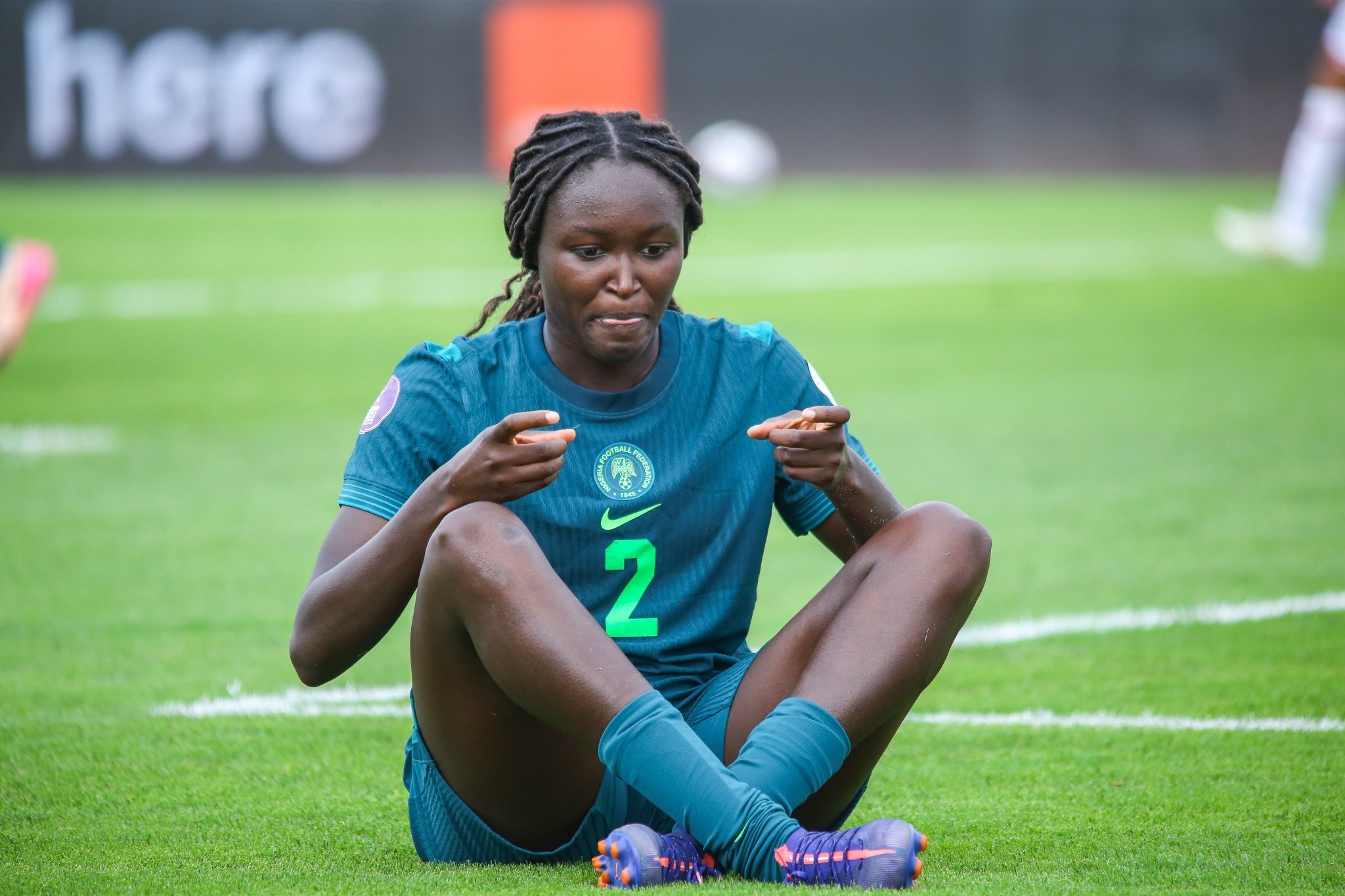
The 2024 Women's Africa Cup of Nations opened with thrilling matches, seeing Nigeria's Super Falcons secure a dominant 3...
Emergence & Dynamics of Nigeria's ADC Coalition

A new opposition coalition, led by the African Democratic Congress (ADC), is emerging to challenge President Bola Ahmed ...
Demise of Olubadan of Ibadanland

Oba Owolabi Olakulehin, the 43rd Olubadan of Ibadanland, has died at 90, concluding a life of distinguished service in t...
Death of Nigerian Goalkeeping Legend Peter Rufai

Nigerian football mourns the death of legendary Super Eagles goalkeeper Peter Rufai, who passed away at 61. Known as 'Do...