AI Serves Up a Better Way to Produce Green Ammonia
Beyond its role as the key ingredient in fertilizers that help feed the world’s 8 billion people, ammonia can also act as a hydrogen carrier. When produced cleanly, it could become a versatile enabler of a future green hydrogen economy, because ammonia is easier to transport and store than the hydrogen it contains. The problem is that virtually all of the world’s 200 million metric tons produced yearly are produced in large energy-intensive factories that consume about 2 percent of the world’s total energy and emit a similar share of global CO2.
But now, researchers at the University of New South Wales Sydney have developed an enhanced way to make green ammonia through electrolysis. The researchers used machine learning to find an innovative catalyst that speeds up the chemical reaction to achieve “a sevenfold improvement in the ammonia production rate,” says Ali Jalili, a senior lecturer at UNSW Sydney and head of the research team. “And at the same time, it is close to 100 percent efficient.”
The new catalyst is designed to improve a lab-built prototype method of making ammonia from air and water using renewable energy. A prototype system, developed in 2021 in collaboration with researchers at the University of Sydney, aimed to produce clean ammonia cheaply on a small scale for decentralized use. To commercialize the process, however, the rate of ammonia production needs to be improved, hence the search for an innovative catalyst.
To formulate the catalyst, the researchers selected 13 prospective metals from which a combination might improve results. “However, that would have meant testing over 8,000 different combinations,” says Jalili. “And once you get past two or three ingredients, the chemistry becomes too entangled for old-fashioned trial and error.”
Instead, they turned to machine learning. The researchers wrote a program in Python based on Gaussian-process learning that can detect patterns in small amounts of data. They fed the program characteristics of the metals functioning as catalysts, as well as their own lab data that considered ammonia production rates, costs, long-term stability, and faradaic efficiency, which is the measure of how effectively electrical energy is used to produce a target product.
When the AI model ran the data and made a suggestion, the researchers conducted an electrolysis test and provided it with feedback, which generated a batch of new suggestions. Four rounds of testing were sufficient to produce 28 candidate experiments to find how adding or removing elements might significantly affect ammonia production performance.
“Running those 28 tests took us less than a week and led straight to an efficient five-metal alloy of iron, bismuth, nickel, tin, and zinc that outperformed every other combination benchmark,” says Jalili. “It greatly reduced discovery time that would have taken months, while improving the process of producing green ammonia sevenfold—exceeding even our most optimistic expectations.”
Ammonia is often produced using an electrolyzer to split water molecules and combine the hydrogen with atmospheric nitrogen. A new catalyst discovered in part through an AI system increases the electrolyzer’s efficiency.University of New South Wales
Next, the alloy was formed into an electrode for use in the earlier lab-built prototype system. The air-water-ammonia module includes a nanosecond-pulsed plasma reactor, an electrochemical cell—now fitted with the new catalyst—and process optimization tools. Dubbed “lightning in a tube” by Jalili, the plasma reactor uses tiny bursts of electricity to energize air and break apart nitrogen molecules, making them reactive enough to form ammonia. The electrochemical cell, meanwhile, speeds up the chemical process that converts the nitrogen compounds into ammonia.
“It’s a hybrid process running on renewable electricity that bridges plasma chemistry and electrochemistry that we developed ourselves,” says Jalili. “Air and water are taken in one end, and from the other side, out comes green ammonia.”
He describes the lab module as a self-contained air-to-ammonia factory packed into a standard 6-meter shipping container. With just air and water, and power from a nearby solar array or wind array, a pilot set-up was able to produce between 50 and 100 kilograms of green ammonia a day—enough to make nitrogen fertilizer for roughly 1 to 5 hectares of crop land depending on the crop. “And extra modules can be added like Lego blocks when more capacity is needed,” says Jalili.
Outside of lab conditions, however, a pilot module being tested on a farm is connected to the grid for stability, rather than being powered by renewable energy. According to Jalili, it is delivering 0.5 kg a day of nitrogen-based fertilizer derived from ammonia—enough to grow 500 cucumber plants in a season. In addition, a much larger system is in the planning stages and backed by the New South Wales state government and commercial partners. It aims to produce 90 metric tons of nitrogen-based fertilizer from ammonia yearly on a farm and will be powered by a solar energy plant of several megawatts. Jalili is also talking with the Bill Gates Foundation about the possible use of the technology to produce fertilizer in the sub-Sahara.
Meanwhile, the researchers are continuing to develop the present system for commercialization. The goal is to shrink the lab set-up down to the size of a suitcase that can produce a couple of kilograms of ammonia a day for under AU $1 million (about US $655,000).
Looking further ahead, Jalili points out that ammonia is one of the world’s most produced chemicals, and the industry knows how to liquefy, store, and ship it safely, while the docking points, pipelines, tank, and terminals are all operating today.
“Our containerized modules will enable renewable energy-rich regions to make green ammonia in real time, instead of waiting for billion-dollar hydrogen plants and supporting infrastructure to be built,” says Jalili. “And the fuel can be used in three ways: as fertilizers, cracked back into hydrogen for fuel-cell vehicles, or burned in turbines and engines for clean back-up power.”
You may also like...
Diddy's Legal Troubles & Racketeering Trial
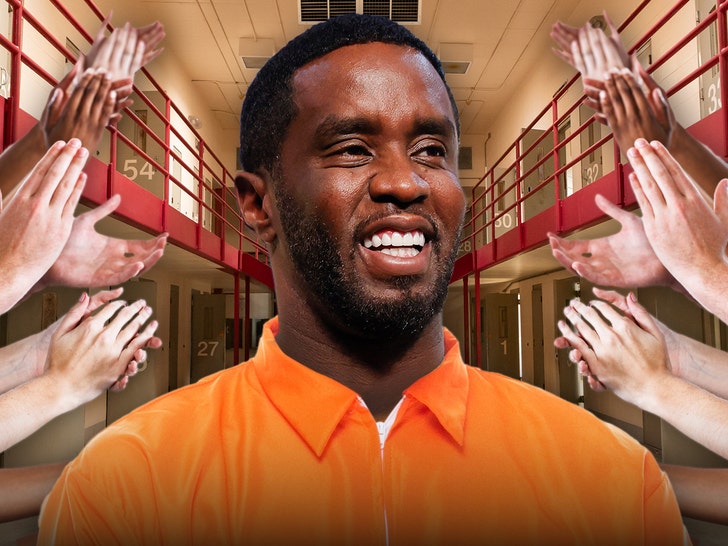
Music mogul Sean 'Diddy' Combs was acquitted of sex trafficking and racketeering charges but convicted on transportation...
Thomas Partey Faces Rape & Sexual Assault Charges

Former Arsenal midfielder Thomas Partey has been formally charged with multiple counts of rape and sexual assault by UK ...
Nigeria Universities Changes Admission Policies
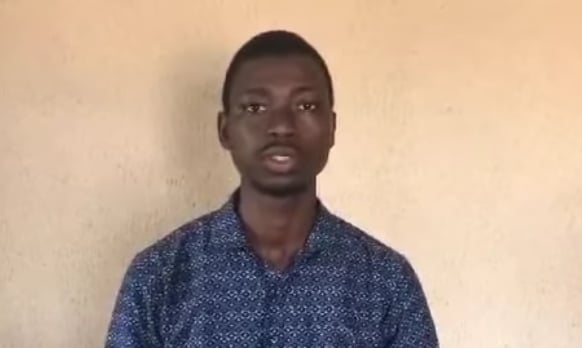
JAMB has clarified its admission policies, rectifying a student's status, reiterating the necessity of its Central Admis...
Ghana's Economic Reforms & Gold Sector Initiatives

Ghana is undertaking a comprehensive economic overhaul with President John Dramani Mahama's 24-Hour Economy and Accelera...
WAFCON 2024 African Women's Football Tournament
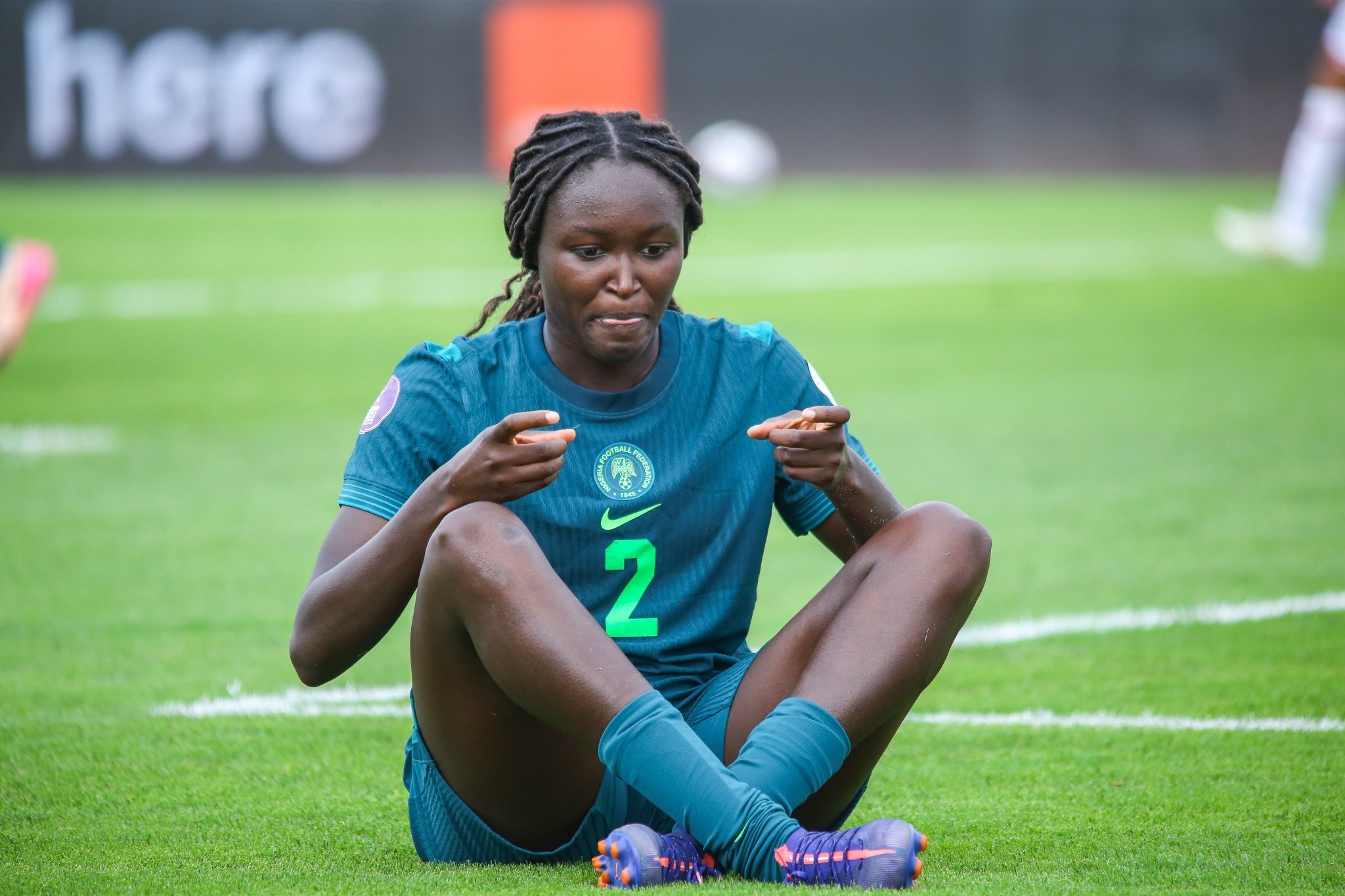
The 2024 Women's Africa Cup of Nations opened with thrilling matches, seeing Nigeria's Super Falcons secure a dominant 3...
Emergence & Dynamics of Nigeria's ADC Coalition

A new opposition coalition, led by the African Democratic Congress (ADC), is emerging to challenge President Bola Ahmed ...
Demise of Olubadan of Ibadanland

Oba Owolabi Olakulehin, the 43rd Olubadan of Ibadanland, has died at 90, concluding a life of distinguished service in t...
Death of Nigerian Goalkeeping Legend Peter Rufai

Nigerian football mourns the death of legendary Super Eagles goalkeeper Peter Rufai, who passed away at 61. Known as 'Do...